Inventory management is an urgent part of maintaining an effective business. Controlling a company’s inventory, which includes raw materials, components, and finished goods, necessitates this role. Powerful stock administration guarantees, there is in every case sufficient stock to fulfill client needs without overloading, which can tie up money and increment stockpiling costs.
Understanding Inventory Management: A Comprehensive Guide
Inventory management is the method involved with supervising and controlling the requesting, stockpiling, and utilization of an organization’s stock. This incorporates overseeing unrefined substances, parts, and completed items. The primary objective is to avoid overstocking, which can clog cash reserves and raise storage costs, and to ensure that there is always enough stock to satisfy customer demand.
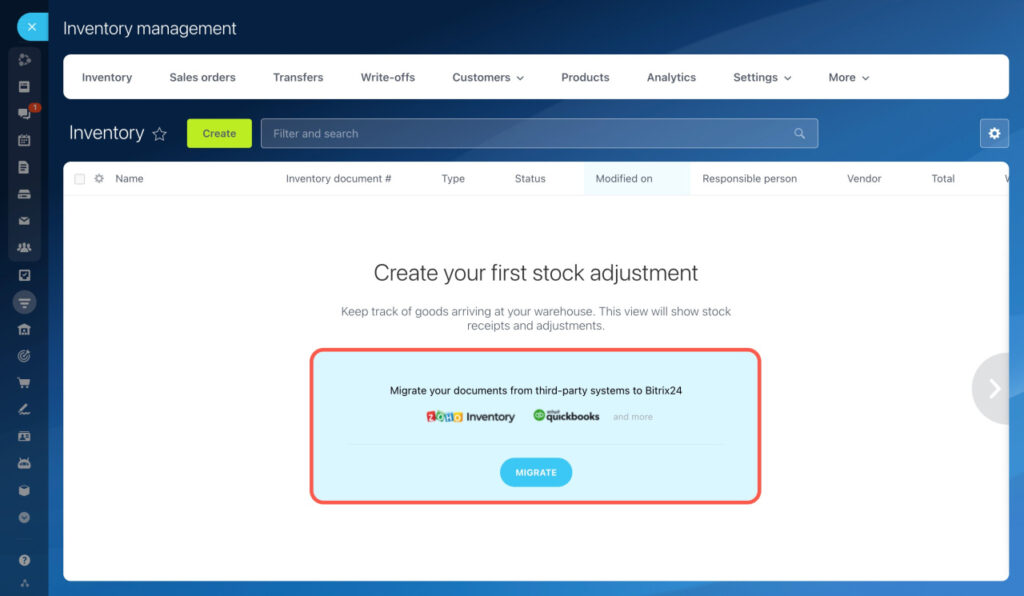
Effective inventory management involves several key elements:
Stock Levels: Maintaining optimal levels of inventory to prevent stockouts and overstocking.
Inventory Tracking: Using systems like SKUs, barcoding, and RFID to keep accurate records of inventory.
Inventory Turnover: Measuring how often inventory is sold and replaced over a period, indicating the efficiency of inventory management.
There are various methods to manage inventory, such as Just-In-Time (JIT), Economic Order Quantity (EOQ), and ABC Analysis, each with its own benefits and applications. Businesses can cut costs, increase cash flow, and improve customer satisfaction by implementing efficient inventory management strategies.
Importance of effective inventory management for businesses
Effective inventory management is crucial for businesses for several reasons:
1. Cost Savings
Reduced Holding Costs: By maintaining optimal inventory levels, businesses can minimize storage costs, insurance, and taxes associated with excess inventory.
Avoidance of Stockouts: Proper inventory management ensures that products are available when needed, reducing the costs associated with emergency orders and lost sales.
2. Improved Cash Flow
Efficient Use of Capital: By not over-investing in inventory, businesses can free up capital for other operations, investments, or emergencies.
Better Financial Planning: Accurate inventory records help in forecasting and budgeting, leading to more informed financial decisions.
3. Customer Satisfaction
Product Availability: Ensuring that products are in stock when customers need them leads to higher customer satisfaction and loyalty.
Timely Deliveries: Efficient inventory management supports timely order fulfillment, enhancing the overall customer experience.
4. Operational Efficiency
Streamlined Processes: Effective inventory management systems can automate and streamline ordering, tracking, and replenishment processes, reducing manual errors and saving time.
Improved Productivity: Employees can focus on more strategic tasks rather than constantly managing inventory issues.
5. Data-Driven Decisions
Accurate Reporting: Real-time inventory data provides insights into sales trends, product performance, and demand patterns, enabling better decision-making.
Forecasting and Planning: Businesses can use historical data to predict future demand and plan inventory accordingly, reducing the risk of overstocking or stockouts.
6. Competitive Advantage
Responsive to Market Changes: Businesses with effective inventory management can quickly adapt to market changes, such as new trends or seasonal demands.
Enhanced Reputation: Consistently meeting customer expectations and maintaining efficient operations can enhance a business’s reputation in the market.
By implementing effective inventory management practices, businesses can achieve significant cost savings, improve cash flow, enhance customer satisfaction, and gain a competitive edge in the market.
Key Elements of Inventory Management
1. Stock Levels
Stock levels refer to the quantity of inventory a business has on hand at any given time. Maintaining optimal stock levels is crucial to ensure that there is enough inventory to meet customer demand without overstocking, which can lead to increased holding costs.
A. Safety Stock
Safety stock is extra inventory kept on hand to prevent stockouts in case of unexpected demand or supply chain disruptions. It acts as a buffer to ensure that there is always enough inventory available to meet customer needs, even if there are delays in replenishment or sudden spikes in demand.
B. Reorder Point
The reorder point is the inventory level at which a new order should be placed to replenish stock before it runs out. It is calculated based on the lead time and the average rate of sales. The formula for the reorder point is:
Reorder Point = (Average Daily Usage × Lead Time) + Safety Stock
C. Lead Time
Lead time is the amount of time it takes for an order to be delivered after it has been placed. This includes the time taken for the supplier to process the order, manufacture or prepare the goods, and ship them to the business. Lead time is a critical factor in determining the reorder point and ensuring that inventory is replenished in a timely manner.
2. Inventory Tracking
Inventory tracking involves monitoring and managing the movement of inventory items from the point of acquisition to the point of sale. Effective inventory tracking ensures accurate stock levels, reduces the risk of stockouts or overstocking, and provides valuable data for decision-making.
A. SKU (Stock Keeping Unit)
A Stock Keeping Unit (SKU) is a unique identifier assigned to each product or item in inventory. SKUs are used to track inventory and manage stock levels efficiently. Each SKU represents a specific item, including its attributes such as size, color, and model. SKUs help in organizing inventory, simplifying the tracking process, and improving accuracy in inventory management.
B. Barcoding and RFID
Barcoding and RFID (Radio Frequency Identification) are technologies used to track and manage inventory.
Barcoding: Barcodes are printed labels with a series of lines and spaces that represent data. Each product is assigned a unique barcode, which can be scanned using a barcode scanner.
Barcoding simplifies the process of tracking inventory by quickly and accurately recording product information, such as SKU, price, and quantity.
It reduces manual errors and speeds up the processes of receiving, storing, and shipping inventory.
RFID (Radio Frequency Identification):
RFID uses radio waves to identify and track inventory items. Each item is equipped with an RFID tag that contains a microchip and an antenna.
RFID tags can be read from a distance without direct line-of-sight, allowing for faster and more efficient inventory tracking.
RFID technology provides real-time data on inventory levels, locations, and movements, enhancing visibility and accuracy in inventory management.
Both barcoding and RFID are essential tools for modern inventory tracking, helping businesses maintain accurate records, streamline operations, and improve overall efficiency.
3. Inventory Turnover
Inventory turnover is a financial ratio that measures how many times a company’s inventory is sold and replaced over a specific period, typically a year. It is calculated using the formula:
\text{Inventory Turnover} = \frac{\text{Cost of Goods Sold (COGS)}}{\text{Average Inventory}}Inventory Turnover=Average InventoryCost of Goods Sold (COGS)
Where:
Cost of Goods Sold (COGS) is the total cost of producing or purchasing the goods that a company sells during a period.
Average Inventory is the average value of inventory during the same period, usually calculated as the sum of the beginning and ending inventory divided by two.
Importance
Inventory turnover is a crucial metric for several reasons:
Efficiency Indicator:
A high inventory turnover ratio indicates that a company is efficiently managing its inventory by selling goods quickly and replenishing stock regularly. This suggests strong sales performance and effective inventory control.
Conversely, a low inventory turnover ratio may indicate overstocking, obsolescence, or weak sales, which can tie up capital and increase holding costs12.
Cost Management:
Efficient inventory turnover helps reduce holding costs, such as storage, insurance, and taxes. It also minimizes the risk of inventory becoming obsolete or damaged.
By maintaining optimal inventory levels businesses can better manage their cash flow and allocate resources more effectively.
Sales and Demand Insights:
Tracking inventory turnover provides insights into sales trends and customer demand. Businesses can use this information to adjust their purchasing and production strategies, ensuring they meet market demand without overstocking.
It helps in identifying slow-moving products that may need promotional efforts or discontinuation.
Competitive Advantage:
Companies with high inventory turnover can respond more quickly to market changes and customer preferences, giving them a competitive edge.
Efficient inventory management can enhance a company’s reputation for reliability and customer satisfaction.
Types of Inventory Management Methods
1. Just-In-Time (JIT)
Explanation: Just-In-Time (JIT) is an inventory management strategy that aims to reduce waste and increase efficiency by receiving goods only as they are needed in the production process. This method aligns raw-material orders from suppliers directly with production schedules, minimizing the amount of inventory on hand.
Benefits:
Reduced Waste: By keeping minimal inventory, businesses can reduce the costs associated with storing and managing excess stock.
Increased Productivity: JIT can streamline production processes and reduce the time and resources spent on managing inventory.
Improved Quality: With smaller, more frequent orders, businesses can better control the quality of materials received1.
Flexibility: JIT allows businesses to quickly adapt to changes in customer demand without being burdened by large amounts of unsold inventory.
2. Economic Order Quantity (EOQ)
Explanation: Economic Order Quantity (EOQ) is a formula used to determine the optimal order quantity that minimizes the total costs of inventory, including ordering, holding, and shortage costs. The EOQ model helps businesses decide how much inventory to order and when to reorder to achieve the lowest possible costs.
Benefits:
Cost Reduction: EOQ helps minimize the total costs associated with ordering and holding inventory.
Efficient Inventory Management: By determining the ideal order quantity, businesses can avoid overstocking and understocking, ensuring a balanced inventory4.
Improved Cash Flow: EOQ allows businesses to better manage their cash flow by reducing unnecessary inventory expenses.
Decision-Making Tool: EOQ provides a systematic approach to inventory management, aiding in more informed decision-making.
3. ABC Analysis
Explanation: ABC Analysis is an inventory management technique that categorizes inventory items based on their importance and value to the business. Items are classified into three categories: A, B, and C. ‘A’ items are the most valuable, ‘B’ items are moderately valuable, and ‘C’ items are the least valuable.
Benefits:
Prioritized Inventory Management: By focusing on the most valuable items (Category A), businesses can allocate resources more effectively and ensure that critical items are always in stock.
Cost Control: ABC Analysis helps in identifying high-value items that require tighter inventory control, reducing the risk of stockouts and excess inventory.
Improved Efficiency: By categorizing inventory, businesses can streamline their inventory management processes and focus on items that have the greatest impact on their operations.
Resource Optimization: ABC Analysis allows businesses to optimize their inventory management efforts, ensuring that resources are used efficiently to manage the most important items.
These inventory management methods each offer unique advantages and can be tailored to fit the specific needs of a business.
Steps to Manage Inventory Effectively
Managing inventory effectively is crucial for any business that deals with physical products. Here’s a detailed breakdown of each step:
1. Define Product Sourcing and Storage Methods
Product Sourcing: This involves identifying reliable suppliers and establishing relationships with them. Consider factors like cost, quality, and delivery times. You might source products directly from manufacturers, wholesalers, or even through dropshipping.
Storage Methods: Decide how and where to store your inventory. This could be in a warehouse, a retail store, or even a fulfillment center. Ensure that your storage methods maintain product quality and facilitate easy access and retrieval.
2. Track Inventory Data
Implement a system to track inventory data in real-time. This can be done using inventory management software that records every transaction, including sales, returns, and restocks. Accurate tracking helps in understanding stock levels, identifying trends, and making informed decisions.
3. Create an Internal SKU System
SKU (Stock Keeping Unit): Develop a unique SKU system to identify each product variant. This system should be logical and consistent, making it easy to locate and manage products. SKUs can include information like product type, size, color, and other attributes.
4. Organize Inventory Storage Areas
Organize your storage areas to maximize efficiency. Use shelving, bins, and labels to keep everything in order. Implement a system like FIFO (First In, First Out) to ensure older stock is sold first, reducing the risk of obsolescence.
5. Use Forecasting to Order Inventory
Use historical data and market trends to forecast demand. This helps in ordering the right amount of inventory, avoiding both overstocking and stockouts. Forecasting tools and software can assist in predicting future sales based on past performance and seasonal trends.
6. Set Up Inventory Receiving Procedures
Establish clear procedures for receiving inventory. This includes checking the received goods against purchase orders, inspecting for damage, and updating inventory records. Efficient receiving procedures ensure that inventory data is accurate from the start.
7. Monitor Inventory Levels
Regularly monitor inventory levels to maintain optimal stock. Use inventory management software to set reorder points and alerts for low stock levels. Regular audits and cycle counts help in identifying discrepancies and maintaining accuracy.
By following these steps, you can streamline your inventory management process, reduce costs, and improve overall efficiency.
Common Inventory Management Terms
Here’s a detailed explanation of each common inventory management term:
Write-Off: A write-off occurs when inventory is removed from the records because it is no longer sellable. This can happen due to damage, theft, obsolescence, or expiration. Writing off inventory helps in maintaining accurate financial records and inventory levels.
Transfer: An inventory transfer involves moving stock from one location to another within the same organization. This could be between warehouses, retail stores, or different departments. Transfers help in balancing inventory levels across locations to meet demand and optimize storage space.
Sales Order: A sales order is a document generated by a seller when a customer places an order for goods or services. It includes details like the quantity, price, and delivery date. Sales orders are crucial for tracking customer orders and ensuring timely fulfillment.
Stock Adjustment: It refers to the process of correcting inventory records to reflect the actual stock levels. This can be due to discrepancies found during audits, returns, or errors in recording transactions. Adjustments ensure that inventory data is accurate and reliable.
Sales: It represent the transactions where goods or services are sold to customers. In inventory management, tracking sales is essential for understanding demand, managing stock levels, and generating revenue. Sales data helps in forecasting and making informed inventory decisions.
These terms are fundamental to effective inventory management, helping businesses maintain accurate records, optimize stock levels, and ensure smooth operations.
Stock Receipt:
- Stock receipt refers to the process of receiving goods or items into a company’s inventory. It involves recording the inflow of products from suppliers or production facilities.
- When goods are received, the inventory manager updates the system to reflect the quantity, cost, and other relevant details of the newly acquired items.
- Stock receipt is crucial for maintaining accurate inventory records and ensuring that the company has the right amount of stock on hand.
Stock Adjustment:
- Stock adjustment is the process of reconciling the recorded inventory levels in the company’s accounts with the actual physical counts of items on hand.
- Reasons for adjusting stock levels include:
- Inventory obsolescence: Removing obsolete or outdated items from inventory.
- Loss: Accounting for theft, spoilage, or damage.
- Recording errors: Correcting mistakes in the amount or number of items received.
- Expiration: Adjusting for items that have reached their expiration date.
- The three prominent forms of adjustments are:
- Decreasing: Reducing inventory due to loss or obsolescence.
- Increasing: Adding stock due to new purchases or corrections.
- Reevaluating: Adjusting inventory for quantity, cost, or overall price.
A seamless inventory adjustment approach ensures real-time recording of changes, prevents errors, and enhances operational efficiency in supply chain management. Remember, maintaining accurate inventory records is essential for efficient operations and financial reporting. 😊📦📊
Benefits of Inventory Management
Effective inventory management offers several key benefits:
Cost Savings: By optimizing inventory levels, businesses can reduce storage costs, minimize waste, and avoid overstocking. Efficient inventory management helps in purchasing the right amount of stock, reducing the need for markdowns and write-offs due to excess or obsolete inventory.
Improved Cash Flow: Proper inventory management ensures that capital is not tied up in unsold stock. By maintaining optimal inventory levels, businesses can free up cash for other operational needs. This leads to better liquidity and the ability to invest in growth opportunities.
Customer Satisfaction: Having the right products available when customers need them enhances customer satisfaction. Effective inventory management helps in meeting customer demand promptly, reducing the chances of stockouts and backorders. Satisfied customers are more likely to return and recommend the business to others.
These benefits contribute to the overall efficiency and profitability of a business, making inventory management a crucial aspect of operations.
Conclusion:
Effective inventory management is crucial for any business dealing with physical products. It helps in maintaining optimal stock levels, reducing costs, improving cash flow, and enhancing customer satisfaction. By accurately tracking inventory, organizing storage, and using forecasting tools, businesses can ensure they have the right products available at the right time.
Implementing effective inventory management practices can significantly benefit your business. It not only streamlines operations but also boosts profitability and customer loyalty. Start by defining clear sourcing and storage methods, tracking inventory data meticulously, and using forecasting to make informed decisions. Regularly monitor and adjust inventory levels to keep your business running smoothly and efficiently. Taking these steps will help you manage your inventory more effectively, leading to a more successful and sustainable business.